The Significance of an Industrial Blade Factory in Modern Industry
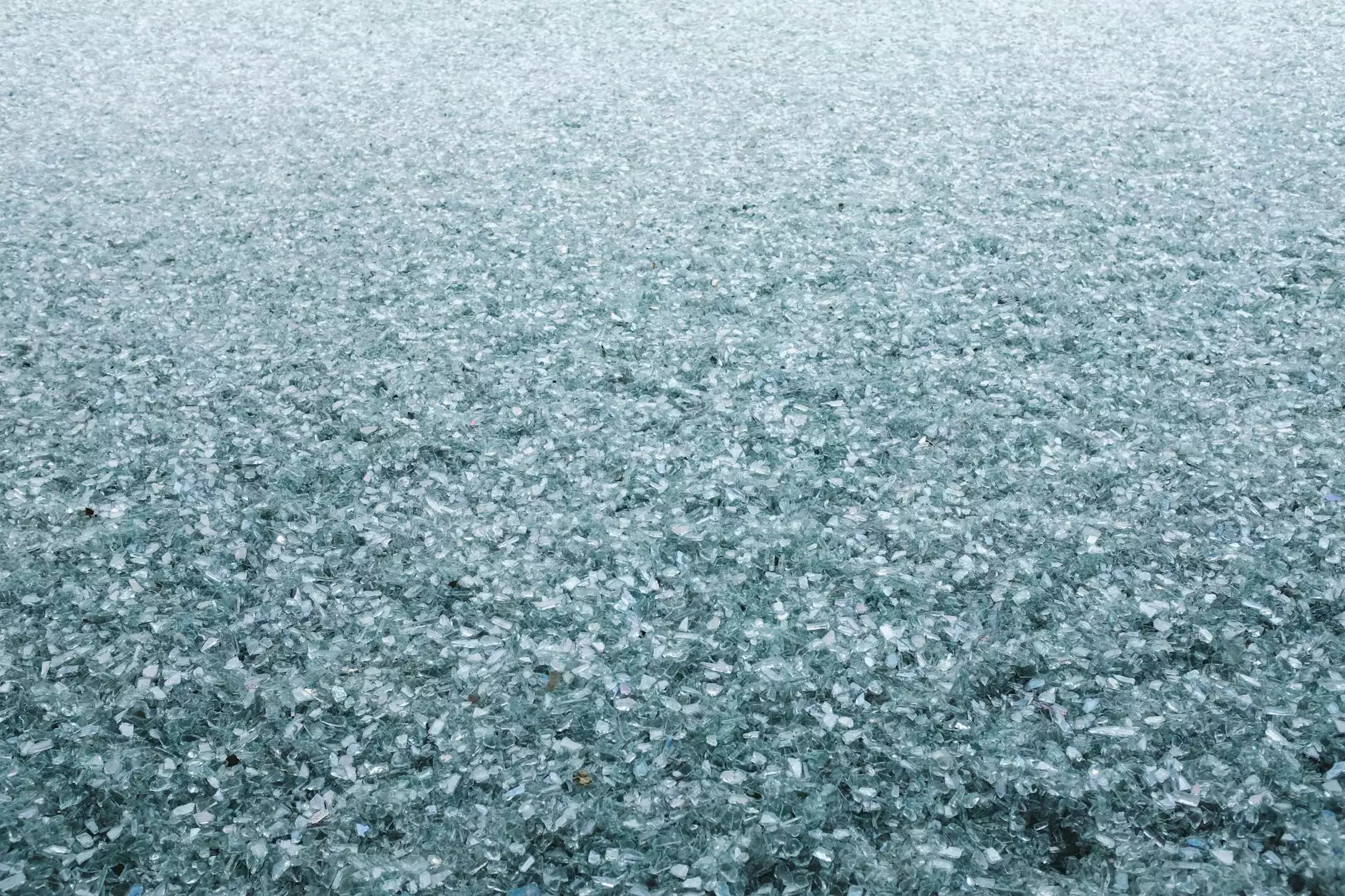
In today’s fast-paced industrial landscape, efficiency and precision are paramount. One pivotal player in enhancing these aspects is the industrial blade factory. These factories specialize in the manufacturing, sharpening, and maintenance of blades used in various sectors including manufacturing, food processing, and logistics. Let's delve into why these factories are integral to business operations and how they can propel companies towards enhanced productivity and profitability.
The Evolution of Blade Manufacturing
The history of blade manufacturing dates back centuries, but the dawn of industrialization brought significant changes. Industrial blade factories have evolved through innovations in technology and production techniques, including:
- Advanced Materials: Modern blades are crafted from high-speed steel, carbide, and other specialized alloys that enhance durability and sharpness.
- Precision Engineering: State-of-the-art machining processes like CNC (Computer Numerical Control) have revolutionized how blades are produced, ensuring every piece meets stringent specifications.
- Quality Control Systems: Factories now employ robust quality controls to track the performance and lifespan of their blades, minimizing defects and maximizing customer satisfaction.
The Benefits of Partnering with an Industrial Blade Factory
Businesses across sectors can realize significant benefits by forging relationships with an industrial blade factory. Here are some noteworthy advantages:
1. Enhanced Operational Efficiency
By utilizing high-quality blades, industries can achieve greater production efficiency. For instance, in the food processing industry, sharp and durable blades reduce downtime caused by blade changes and maintenance issues, ensuring a smoother operation.
2. Cost-Effectiveness
While the initial investment in high-quality blades might be higher, the long-term savings are substantial. Industrial blade factories provide blades that last longer and require less frequent replacement, ultimately lowering operational costs.
3. Customization Options
Many industrial blade factories, including those like szblade.com, offer customization services that cater to the specific needs of various industries. This can include:
- Custom blade shapes and sizes
- Specific edge treatments for enhanced performance
- Tailored material choices for unique applications
4. Professional Knife Sharpening Services
Not only do these factories manufacture blades, but they also often provide professional knife sharpening services. Regular sharpening extends the lifespan of blades and maintains optimal cutting performance, essential for any business relying on cutting tools.
The Role of Technology in Blade Manufacturing
As industries embrace the fourth industrial revolution, technology plays a critical role in the operations of an industrial blade factory. Some key advancements include:
1. Automation in Production
Automation has drastically enhanced productivity in blade manufacturing. Automated machinery and robotic arms can produce blades with unparalleled speed and precision, allowing factories to scale operations quickly.
2. Computer-Aided Design (CAD) and Simulation
CAD software allows engineers to devise intricate blade designs, while simulation tools help predict how blades will perform under various conditions, ensuring that the final product meets all performance criteria.
3. Advanced Coating Technologies
Coatings such as titanium nitride and diamond-like carbon make blades more resistant to wear and tear. These coatings not only enhance the longevity of blades but also reduce friction, leading to superior cutting performance.
The Importance of Sustainability in Blade Factories
With the growing global emphasis on sustainability, industrial blade factories are adapting their practices to minimize environmental impact. Here’s how they’re making strides:
1. Eco-Friendly Materials
Many factories are shifting towards sourcing materials that are recyclable or less harmful to the environment. This includes using high-quality alloys that can be reprocessed without degrading performance.
2. Waste Reduction Techniques
Implementing lean manufacturing principles allows factories to reduce waste throughout the production process. Whether it's minimizing scrap material or optimizing resource use, these strategies not only lower costs but also benefit the environment.
3. Energy Efficiency
Investing in energy-efficient machinery and optimizing production schedules help reduce the carbon footprint of industrial blade factories. Factories are also increasingly using renewable energy sources to power their operations.
Quality Assurance Standards in Blade Manufacturing
Quality should never be compromised when it comes to blade manufacturing. Industrial blade factories implement rigorous quality assurance (QA) protocols to ensure the highest standards are met. These protocols commonly include:
- Material Inspection: All raw materials undergo testing to confirm their purity and performance characteristics.
- Dimensional Checks: Regular inspections during production ensure all blades meet specifications.
- Performance Testing: Finished products are subjected to tests simulating real-world usage to validate their effectiveness.
Choosing the Right Industrial Blade Factory
Selecting a reliable industrial blade factory is crucial for businesses looking to enhance their operations. Here are factors to consider when making your choice:
1. Proven Expertise
Look for factories with a significant track record in blade manufacturing and a solid reputation in your specific industry. References and case studies can provide insight into their capabilities.
2. Certification and Compliance
Ensure the factory adheres to relevant industry standards such as ISO certifications, which signify a commitment to quality and safety in production processes.
3. Customer Support
Outstanding customer service can make a significant difference, especially when it comes to custom orders and technical support regarding blade usage and maintenance.
Future Trends in Industrial Blade Manufacturing
The future of industrial blade factories is poised for further transformation. Emerging trends to watch include:
1. 3D Printing
As additive manufacturing technologies evolve, 3D printing is becoming a viable method for producing specialized blades rapidly. This could significantly reduce lead times and allow for unprecedented customization.
2. Data Analytics
Employing data analytics enables manufacturers to forecast demand accurately, optimize inventory management, and improve overall operational efficiency.
3. Integrating Machine Learning
Machine learning can be applied to analyze production patterns and predict maintenance needs, thus enhancing the lifespan and performance of machinery used in blade manufacturing.
Conclusion
In summary, industrial blade factories like szblade.com play a critical role in driving efficiency and innovation across various industries. Their commitment to quality, technology, and sustainability not only enhances operational productivity but also ensures that businesses can meet the demands of a competitive marketplace. As industries continue to evolve, the significance of reliable, high-performing blades will only become more pronounced.
By leveraging the strengths of an industrial blade factory and embracing advancements in technology, businesses position themselves for long-term success and sustainability. It is clear that investing in superior blade manufacturing and maintenance services is an essential step in maintaining a competitive edge in today's ever-changing industrial landscape.