Understanding Injection Mold Companies: A Deep Dive into Metal Fabrication
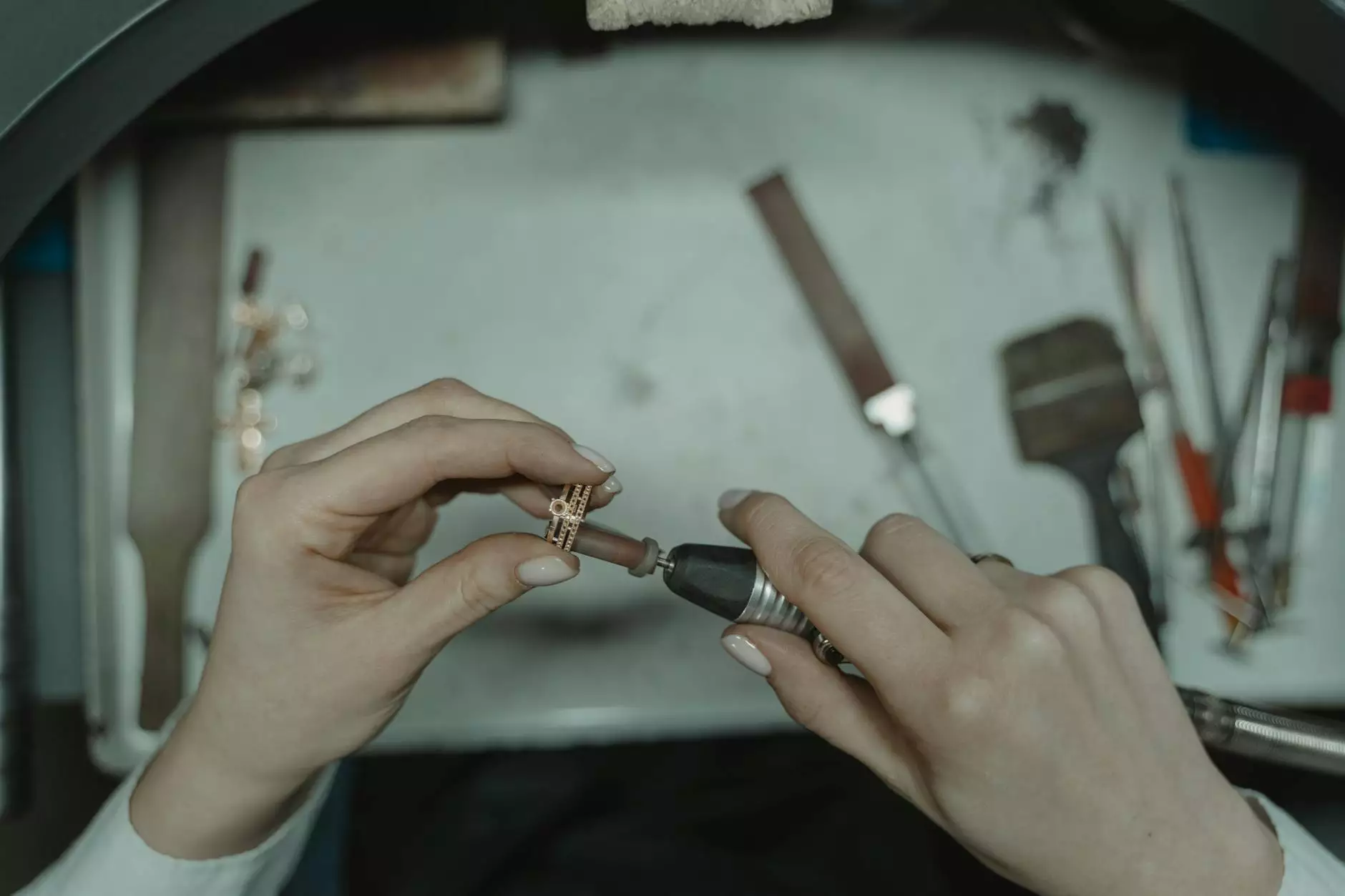
In the ever-evolving landscape of manufacturing, injection mold companies hold a pivotal position, especially in the realm of metal fabrication. With advancements in technology and techniques, these companies have transformed the production capabilities of various industries, delivering precision-engineered components that meet the growing demands of consumers and businesses alike.
What is an Injection Mold Company?
An injection mold company specializes in designing and manufacturing molds that create parts through a process called injection molding. This method involves the injection of molten material, which can be metal, plastic, or other substances, into a mold cavity. The material cools and solidifies to form the desired shape.
The Importance of Injection Molding in Metal Fabrication
Injection molding is particularly important in the field of metal fabrication for several reasons:
- Efficiency: Injection molding allows for rapid production of parts, significantly reducing the time required to bring a product to market.
- Cost-Effectiveness: Once the initial mold is created, producing consistent parts requires minimal labor and material.
- Precision: Injection molding enables the creation of intricate designs and precise dimensions, essential for high-quality metal components.
- Material Versatility: While traditionally associated with plastics, advancements in technology have enabled injection molding processes for various metals, enhancing its application scope.
Key Processes in Injection Molding
The process of injection molding involves several crucial steps, each contributing to the final product's quality and durability. Here are the essential phases:
1. Design and Prototyping
The first step is the design of the mold. Engineers utilize CAD (Computer-Aided Design) software to create detailed mold designs. Prototyping may take place to test the mold and ensure it functions as intended.
2. Material Selection
Choosing the right material is vital for the success of the molding process. Factors such as strength, thermal properties, and cost must be considered. Common materials used in metal injection molding include:
- Stainless Steel
- Titanium Alloys
- Copper Alloys
- Tool Steel
3. Mold Fabrication
Once the design is finalized and materials selected, the mold itself is fabricated. This typically involves precision machining techniques to create the mold cavities.
4. Injection Molding Process
The actual injection molding process begins with the heating of the metal until it becomes molten. The molten metal is then injected into the mold under high pressure, ensuring it fills the cavities uniformly.
5. Cooling and Solidification
After injection, the material is allowed to cool and solidify within the mold. This step is critical as it sets the final shape and structural integrity of the part.
6. Demolding and Finishing
Once the part has cooled sufficiently, it is extracted from the mold. Additional finishing processes may be required, such as machining, polishing, or coating, to achieve the desired surface finish and characteristics.
Why Choose a Reliable Injection Mold Company?
Partnering with a reputable injection mold company can significantly impact your production quality and efficiency. Here are several reasons to consider:
- Expertise: Established companies possess extensive experience, ensuring they can handle complex projects with ease.
- Quality Assurance: A reliable company implements stringent quality control measures, resulting in products that meet or exceed industry standards.
- Customer Support: A good injection mold company provides valuable support throughout the project lifecycle, from design to after-sales service.
- Technological Advancements: Leading companies continuously invest in state-of-the-art technology to enhance their capabilities and maintain competitive advantages.
Applications of Injection Molded Metal Components
The versatility of injection molded metal components makes them suitable for various industries and applications, including:
- Automotive: Production of parts such as brackets, housings, and gears that require high strength and precision.
- Aerospace: Fabrication of lightweight yet durable components critical for aircraft performance and safety.
- Electronics: Creation of intricate parts such as heat sinks and structural components used in electronic devices.
- Medical Devices: Manufacturing precise components that are essential for medical technologies and equipment.
The Future of Injection Molding in Metal Fabrication
The future of injection molding, particularly in metal fabrication, looks 🌟 promising. With ongoing technological advancements, we can expect the following trends:
1. Increased Automation
Automation is set to revolutionize the injection molding process, enhancing production speed and precision while minimizing human error.
2. Sustainable Practices
As environmental concerns grow, injection mold companies are exploring sustainable materials and processes to reduce waste and energy consumption.
3. Impact of Industry 4.0
The integration of IoT (Internet of Things) and AI (Artificial Intelligence) in manufacturing is poised to optimize injection molding processes, leading to greater efficiency and product quality.
4. Advanced Material Development
Research into new alloys and composites will enable injection mold companies to create even more versatile and high-performance components.
Partnering with DeepMould.net
If you are searching for a reliable injection mold company, look no further than DeepMould.net. With extensive experience in the metal fabrication industry, DeepMould provides:
- High-quality mold design and manufacturing services
- A commitment to precision and client satisfaction
- State-of-the-art facilities equipped with the latest technology
- Comprehensive support throughout the entire project lifecycle
Conclusion
In conclusion, injection mold companies play a crucial role in advancing the metal fabrication industry. Through their expertise in injection molding technology and commitment to quality, these companies enhance the efficiency and capability of modern manufacturing processes. As we move forward, innovations in materials, automation, and sustainable practices will continue to shape the future of this vital industry. Partnering with a knowledgeable and experienced company like DeepMould.net can ensure that your manufacturing needs are met with excellence and precision.